Introduction
The oldest division of Dalal is the Chemicals Division. The products in the Chemical Division range from Rotary Vacuum Dryers to Wiped Film Evaporators.
Wiped Film Evaporator
Introduction
The Wiped Film Evaporator is used for concentration, distilling, stripping, dehydration and deodorisation of products which are heat sensitive or viscous. The equipment can handle a very wide range of feed compositions ranging from 1% to over 95% concentration. WFE has several advantages as stated in the table below. The operation is continuous with a single pass; the self cleaning continuous contact wipers produce and renew the thin film. Such an operation improves product yield, avoids residue and colour formation. It has an internal condenser (optional) that minimizes the pressure drop and maintains vacuum.
Working Principle
The operation process in the WFE is simple but yet effective. Feed is introduced at the top of the unit and spread on the shell inner surface by the rotating distribution plate. Specially designed wipers wipe the feed thus creating and renewing the film. This thin film enables an efficient heat transfer even for highly viscous fluids. The low boiling component evaporates and passes through an entrainment separator. This minimizes the carry over of liquid droplets along with the vapors. The vapors are removed through the vapor line to an external condenser (optional) and condensed. For specific applications which demand low pressure drop, the central section of the evaporator is provided with a condenser, thus making the unit a short path/molecular distillation unit. In this case, the vapors are allowed to condense on the outside of the tube bundle and flow out of the vaporator via the condensate outlet provided at the centre.
The high boiling component flows along the shell wall and is discharged from the product outlet. Wiper action is important in promoting downward flow. The product/concentrate should be in fluid form at the operating temperature. Different designs of rotors are available depending upon the product, its viscosity and the process pressure.
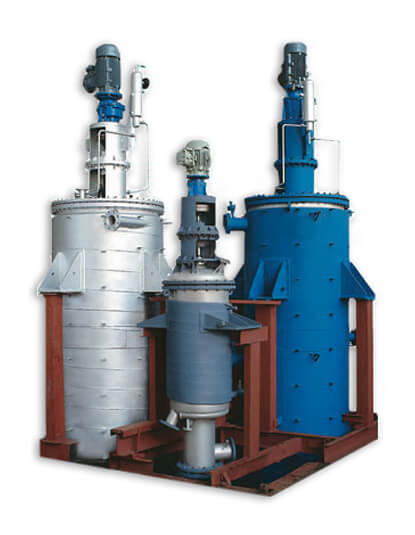
Milestones
Advantages
- Evaporation at low operating temperature
- Short residence time (few seconds)
- High heat transfer coefficients
- Low pressure drop on vapor side
- No degradation or loss of active ingredients
- Self cleaning\wiping of the heat transfer surface
- Suitable for viscous liquids
- Continuous operation
- Low maintenance
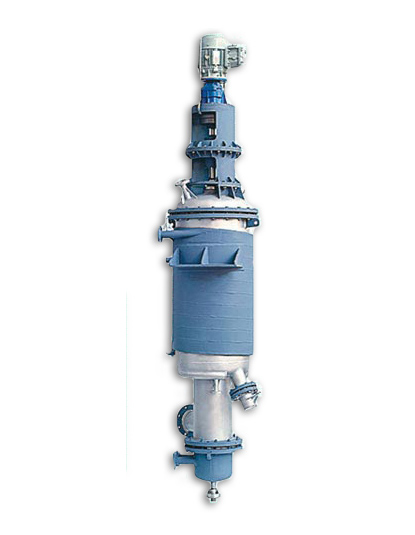
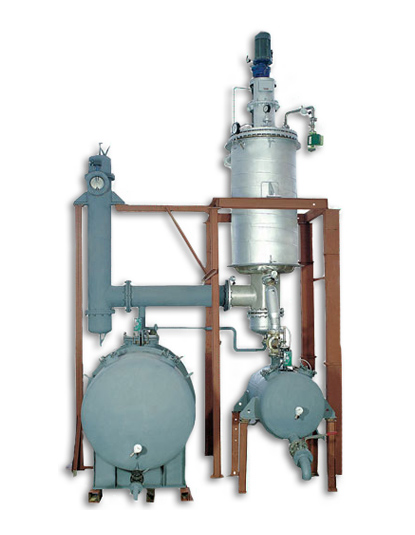
Features
- Low rotational speed
- No bottom bearing
- Higher power to take care of feed fluctuations
- Chevron rotor with interchangeable panels for ease of cleaning
- Double groove gasket for high vacuum WFE
- Conical bottom with auger
- Top vapour outlet/li>
- Large internal condenser
- Swing / Hinge wiper blades
- Open rotor (no entrainment separator)
Falling Film Evaporator
A Falling Film Evaporator is used for concentration and evaporation of relatively low viscosity liquids. Steam, hot water or hot oil is used as the heating media and the process is carried out under atmospheric or vacuum condition. The Evaporator is used for volume reduction where dilute products are concentrated to a medium concentration. The process is continuous. The liquid to be concentrated is fed from the top and a distributor ensures proper feed distribution in each of the tubes. The distributor also ensures that all tubes are wetted and that the liquid flows in a film. The liquid and vapour both travel vertically downward. Due to a relatively thin film, the heat transfer coefficient is better than that obtained in reactors and simple shell and tube evaporators. If further concentration is required, the concentrated product can then be fed to the WFE.
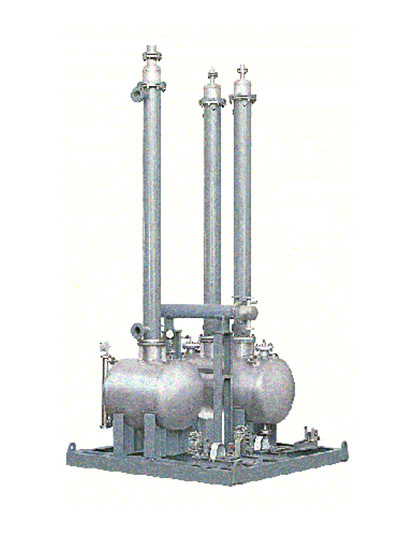
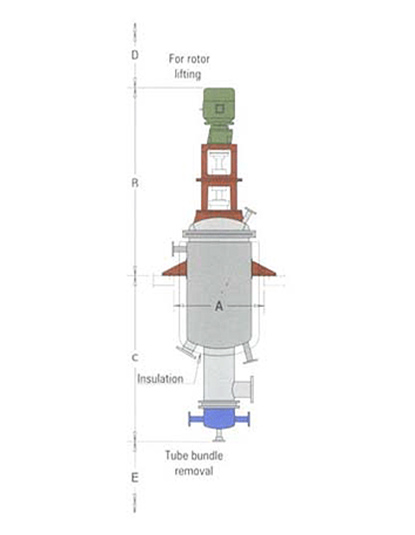
Total Solutions
Dalal Engineering supplies complete systems consisting of one or more wiped film evaporators, falling film evaporators, auxiliary condensers, sub-coolers, receivers for residue and concentrate, vent condenser, vacuum system, interconnecting piping with instrumentation, valves etc.
A prototype Wiped Film Evaporator system is available at its Thane factory where trials can be conducted to determine feasibility and equipment with guaranteed performance can be offered.
Technical Specifications | ||||||||
Evaporator area m2 | 0.45 | 1.0 | 2.0 | 3.0 | 5.0 | 7.5 | 12.0 | 20.0 |
A (Square Cut-Out) | 660 | 1010 | 1010 | 1320 | 1320 | 1320 | 1650 | 1895 |
B | 1190 | 1710 | 1760 | 1800 | 1885 | 2249 | 2604 | 3360 |
C | 616 | 1295 | 1770 | 1460 | 2205 | 2877 | 3590 | 5155 |
D | 480 | 900 | 1200 | 1130 | 1190 | 2600 | 3000 | 2050 |
E | 600 | 1000 | 1900 | 1690 | 2100 | 3000 | 3625 | 4000 |
Other sizes available as per requirement. Internal condenser optional. |
Rotary Vacuum Dryers
Introduction
Rotary vacuum dryers offer clean, simple and effective method of drying wet cake, powder and even slurry. Labor and energy costs are minimal compared to tray dryers and product losses during handling are also negligible. Additionally valuable organic solvents can be conveniently condensed and recovered.
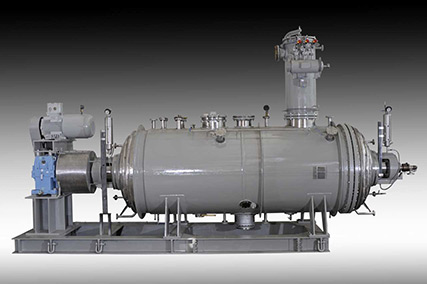
Working Principle
The drying in a rotary vacuum dryer is a batch operation under vacuum. It is possible to dry heat sensitive materials at well below boiling points of water and solvents. Drying time depends on material being dried, amount of solvent or water to be removed, desired final moisture content, permissible jacket temperature etc. The dryer is available in sizes ranging from 100 liters to 20,000 liters gross volume. The volume of wet material loaded into the dryer is usually restricted to 40-45% of gross volume.
Salient Features
- Equipped with different designs of agitators depending on the material to be dried.
- Unique quick opening discharge valve permits direct packing of dry product into bags or drums.
- Breaker rods are provided to prevent lump formation and allow quick and complete drying.
- Shaft sealing by mechanical seals is also available.
- N2 pulse jet dust filter (self cleaning type).
- Sampling value sizes range from 100 LT. to 1600 LT. gross volume.
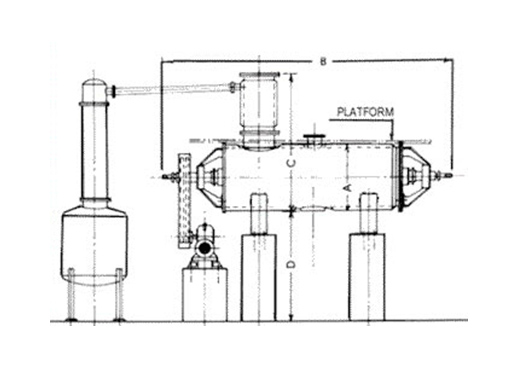
Supertor
Introduction
Supertor is a high shear pump like machine to handle Liquids & Slurries. It has saw tooth construction Stator & Rotor arrangement. This creates strong turbulence which can be used for achieving - Homogenizing, Grinding, Crushing, Delumping, Dissolution, Maceration, etc.
Working Principle
The Supertor can crush, grind, homogenize & pump. An angular disc rotates in a cylindrical housing. Notched teeth in the Rotor disc meshes with teeth of Stator to effect disintegration & crushing - thus resulting movement generates thrust & shear stress causing acceleration of medium in both – axial & radial direction, resulting in intense mixing with pumping of the medium.
Supertor Applications
|
|
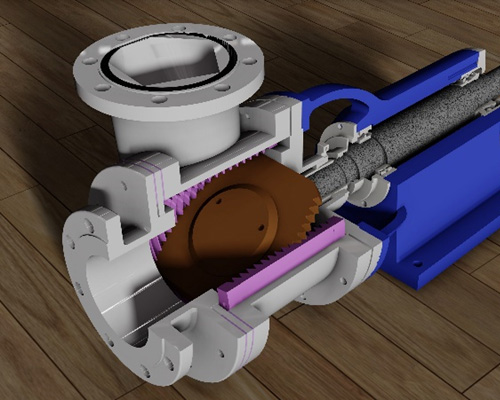
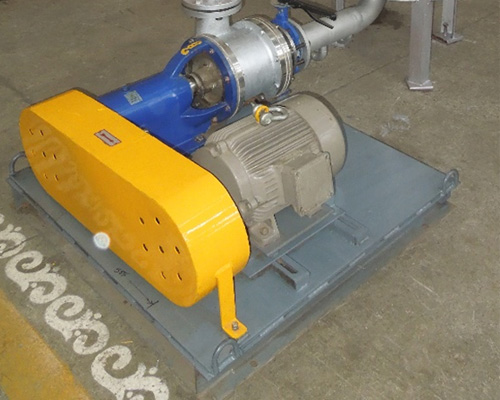
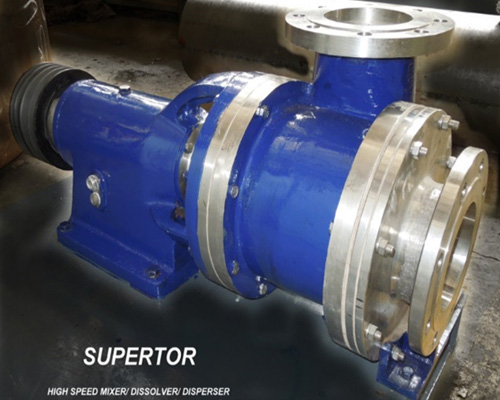
Dimensions | |||||
Size | Suction | Discharge | L | W | H |
22 | 100 | 100 | 1000 | 1020 | 497 |
25 | 150 | 150 | 1120 | 1250 | 572 |
Drum Flakers
Introduction
Drum flakers (also known as cooling drums) are used for solidifying molten material. After Flaking operation, the material forms Flakes a form easily handled and is further processed or packed into containers for transport.
A great advantage of flakers is that they offer a continuous process.
Working Principle
The Cooling Drum dips in pool of Molten liquid in Trough (direct immersion), or indirect immersion using doctor/applicator rolls. The molten liquid is cooled on the outer surface of cooling drum and after a partial revolution; the cooled and solidified product is removed by a scraper in the form of flakes. The cooling drum of the flaker is specially designed to provide an even cooling effect by having uniform and effective internal distribution of media. As a result, both high output and uniform flakes are produced.
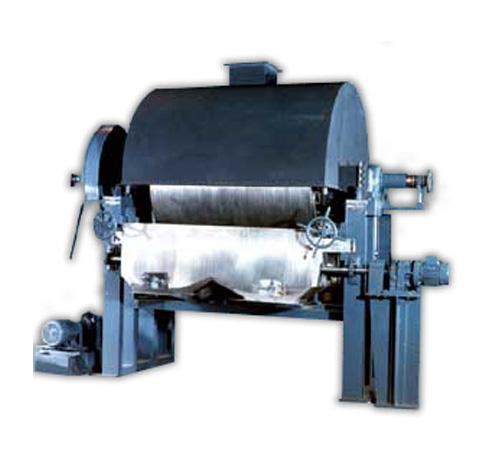
Salient Features
- Variable speed drive arrangement for adjustment of the drum speed for optimum performance.
- Suitable for a wide range of chemical and pharmaceutical products.
- Contact parts can be stainless steel, carbon steel, and hard chrome plated depending on material requirements.
- GMP design
- Flake Thickness Control
- Drum Water Cooling – Spray Type Arrangement with Siphon Assist Compressed Air
- Type of Enclosure – Simple Canopy, Fully Closed Type, suitable for Gas Purging, etc
- Blade Movement – Hand Wheel, Geared Hand Wheel, Pneumatic Operated
- Chute – Multi Bagging Points, Screw Conveyor
- Instruments – Temperature Measurements, Trough Level, Water Flow Measurement, Others
- Drum Speed Variation – Mechanical Type & Variable Frequency Drive
- Customization as per Design Needs
- Tilting Trough to facilitate easy cleaning while change of Product
- Low Hold up trough
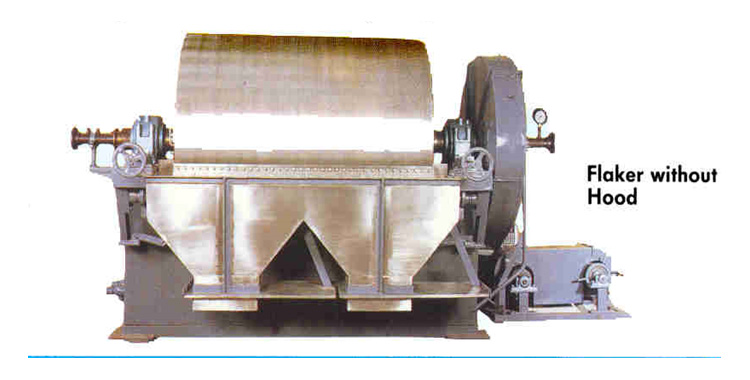
Vibro Energy Seperators
Introduction
Vibro Energy Seperators are used for screening and grading of dry powders and screening of slurries. The machine is a proven performer for applications as diverse as abrasives, ceramic powders and slurries, chemicals, pharmaceuticals, powder coatings and slurries, minerals, metal powders, and food products.
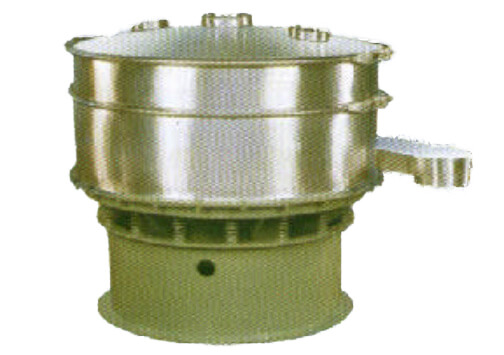
Working Principle
The machine is a rigid screening device that vibrates about its center of mass. Vibration is achieved by mounting eccentric weights on the top and bottom of a special heavy-duty motor with extended shafts on both its ends. Vibration can be varied by addition or removal of auxiliary weights and by changing the angle between the top and bottom eccentric weights. This allows control of amplitude as well as material flow patterns.
Salient Features
- Low power, space and maintenance requirements
- High separation efficiency
- Separation achieved using meshes as fine as 500 mesh
- Multi-deck arrangements with up to 7decks for special applications
Technical Specifications | |||||||||||
Size | Motor HP/KW |
A (mm) |
B (mm) |
C (mm) |
D (mm) |
E (mm) |
F (mm) |
G (mm) |
H (mm) |
I (mm) |
J (mm) |
48 cms | 0.25/0.186 | 495 | 450 | 695 | 580 | 810 | 1000 | 1130 | 100 | 554 | 360 |
66 cms | 1/0.75 | 673 | 600 | 875 | 745 | 1005 | 1160 | 1245 | 127 | 740 | 482 |
80 cms | 1/0.75 | 813 | 510 | 802 | 665 | 939 | 1100 | 1210 | 150 | 898 | 582 |
120 cms | 2/1.5 | 952 | 520 | 872 | 705 | 1040 | 1233 | 1343 | 152 | 1195 | 730 |
150 cms | 2/1.5 | 1105 | 535 | 885 | 710 | 1075 | 1265 | 1375 | 203 | 1502 | 927 |
Trial Facility
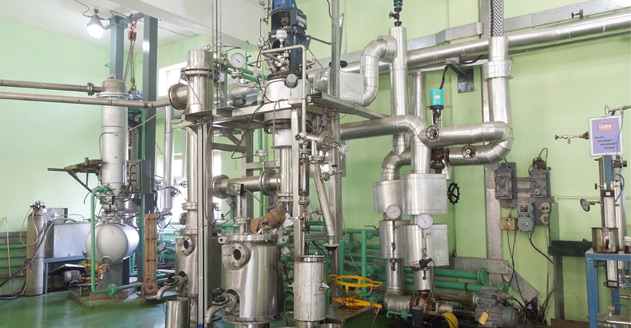
A prototype system is available at its Thane Factory where trials can be conducted to determine feasibility, and equipment with guaranteed performance can be offered.
Wiped Film Evaporator | |||||
Size | M.O.C | Qty. Required For Trial | Qty. Of Tamples Required For Testing | Pressure Rating | Remarks |
0.45 m² | SS-316 | 50 to 100 litres | 200 Ltrs. | Shell- Full vacuum Jacket – 6 kg/cm²g (steam) | Typical throughput for aqueous material is about 60 to 100 kg/hr. |
Parameters
Vacuum – water Ring vacuum pump at approx. 700 mm Hg. Piston Pump with Booster – 0.5 mm Hg A. Hot Media – Steam Heating – 100 to 180 ºC or Hot Oil Heating range 100 to 320 ºC Cooling Media – Cooling Tower Water |
|||||
ATFD | |||||
Size | M.O.C | Qty. Required For Trial | Qty. Of Tamples Required For Testing | Pressure Rating | Remarks |
0.5m² | SS-316 | 30 – 50 ltr/hr. | 200 Ltrs. | Shell- Full vacuum Jacket – 6 kg/cm²g (steam) | Typical throughput for aqueous material is about 30 to 60 kg/hr. |
Vibro Energy Seperators | |||||
Size | M.O.C | Qty. Required For Trial | Qty. Of Tamples Required For Testing | Pressure Rating | Remarks |
19” dia | SS-304 | 30 lit | 20 to 50 kgs | Meshes from 1/2” to 350 available. | Throughput is in the region of 50 to 100 kg/hr depending upon particle size distribution. |
Utilities | Steam | Boiler : 200 kg / hr, 6 kg / cm2g |
Hot water | Hot water circulation system is available with appropriate pump and temperature control. | |
Thermopack | Suitable for, 320°C. | |
Vacuum | a) 100 m²/hr. double stage water ring vacuum pump with air jet booster. b) 100 m3/hr oil seal vacuum pump. c) 125 m3/hr Rotary piston pump. d) 1000 m3/hr Booster roots blower. |
|
Cooling water | a) Water at ambient temperature from cooling tower. b) We can arrange chilled water circulation between 8 to 12° C for condensation of lower boiling materials. |
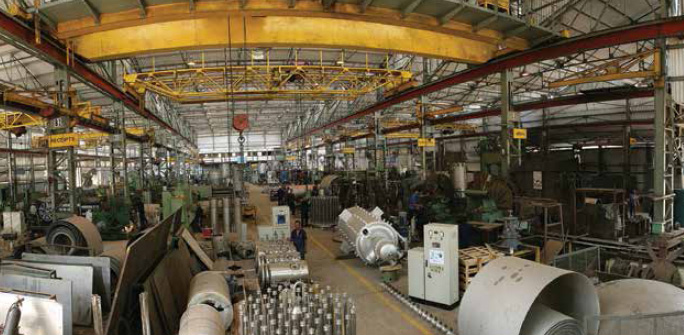